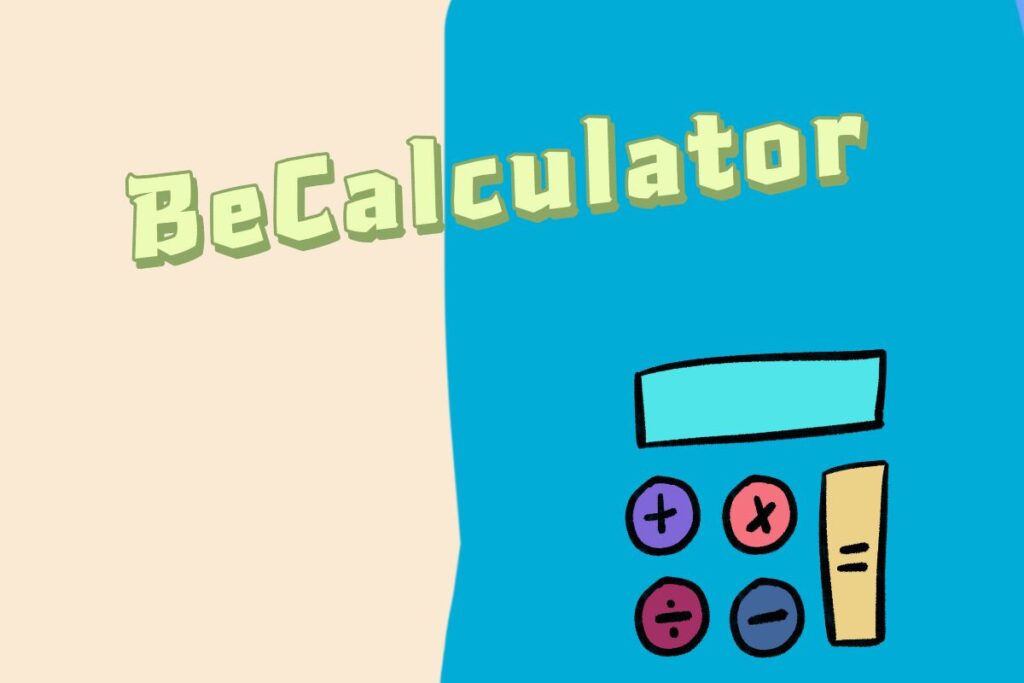
BECALCULATOR CONVERTER
Online unit converter: It is very convenient to realize the functions of length unit conversion, weight conversion conversion, time unit conversion and so on. You can use this converter to convert any unit you need. As shown in the calculator below: Enter the number you want to convert on the left, and the result will appear on the right.